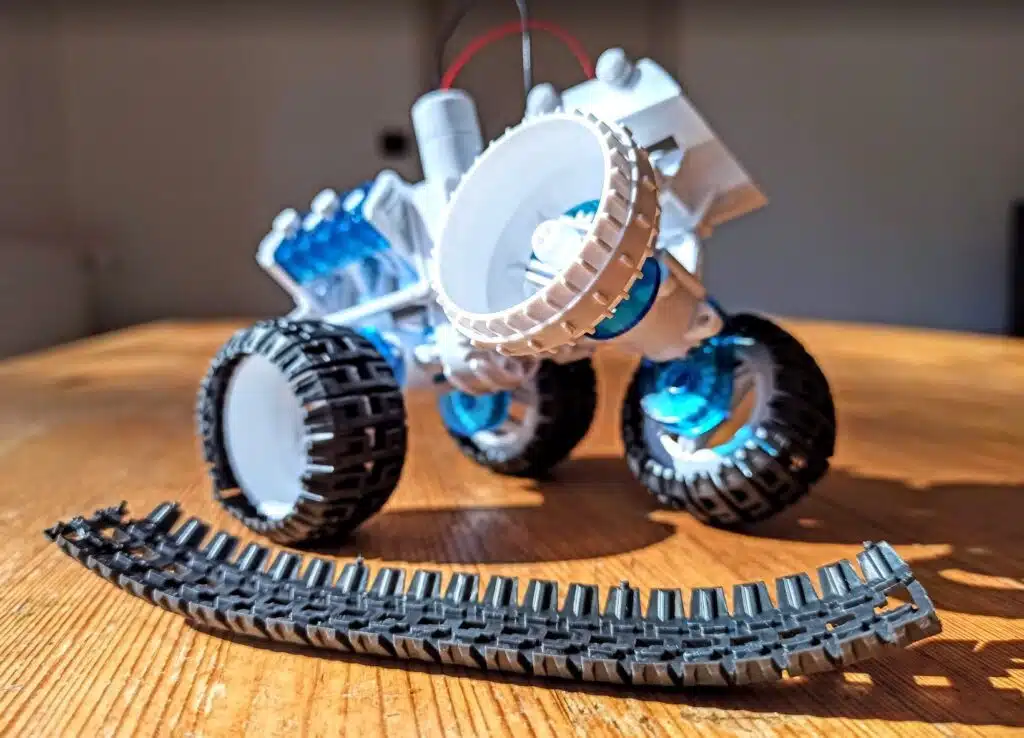
1. Présentation générale du processus d’injection plastique
2. Comment éviter les principaux défauts liés à l’injection plastique ?
3. Quelle matière choisir pour un boitier électronique avec PCB ?
La conception d’une pièce en plastique est un travail à considérer dans son ensemble : le dessin 3D de la pièce doit se faire en anticipant les problèmes d’injection ou de fabrication des moules.
- Fonction de la pièce : esthétique ou technique ?
- Contraintes d’assemblage : choix et respect des tolérances de montage
- Résistance mécanique, matériau, environnement…
Outre les problèmes fonctionnels et structurels, les contraintes de mouillabilité sont à étudier dès le début de la conception. Il faudra anticiper au maximum la manière dont le plastique fondu remplit et se refroidit dans le moule.
1. Présentation générale du processus d’injection plastique
Avantages liés à la production par injection :
- La production de gros volumes de pièces
- Il est possible de produire plusieurs pièces à chaque cycle (moules à plusieurs empreintes)
- Une bonne précision de la tolérance
- Une bonne finition
- La répétabilité, réduit le taux de production défectueuse dans la fabrication en série de formes plastiques difficiles
- la production en série de produits en plastique garantie une efficacité élevée et un gaspillage minimal de ressources
Inconvénient :
- L’investissement initial pour la fabrication des outils
Le processus de moulage par injection comporte cinq étapes principales
1. Le serrage : L’unité de serrage maintient les deux moitiés du moule d’injection ensemble pendant l’injection et le refroidissement.
2. L’injection : Le plastique est injecté dans le moule à travers une buse d’injection. Pendant la phase d’injection, une matière plastique, généralement sous forme de granules, est chargée dans une trémie au-dessus de l’unité d’injection. Les pellets sont introduits dans un cylindre où ils sont chauffés jusqu’à ce qu’ils atteignent la forme fondue. Dans le cylindre chauffant, il y a une vis ou un piston motorisé qui mélange les pellets fondus et les force à l’extrémité du cylindre. Une fois que suffisamment de matériau s’est accumulé devant la vis, le processus d’injection commence. Le plastique fondu est inséré dans le moule à travers une carotte, tandis que la pression et la vitesse sont contrôlées par la vis.
3. Le refroidissement : Le plastique refroidit jusqu’à sa forme solide dans le moule.
4. L’ouverture du moule : l’unité de serrage s’ouvre et sépare les deux moitiés du moule.
5. L’éjection : les éjecteurs sortent la pièce finie du moule. Les carottes non utilisées peuvent être recyclées.
Outillages et matières nécessaires à la production en plasturgie
La presse à injecter
La presse comprend deux unités principales :
- Unité d’injection : avec la trémie, le vérin d’injection, la vis sans fin et l’appareil de chauffage.
- Unité de serrage : où l’on placera le moule interchangeable d’une pièce
Les presses d’injection sont classées par tonnage, ce qui correspond au calcul de la force d’ouverture du moule sous pression. Si le matériau plastique est très rigide, le remplissage du moule nécessitera plus de pression d’injection.
Le moule
Le moule (ou matrice) est l’élément modulaire de l’outillage. Il est spécifique à chaque pièce produite et se compose généralement de deux parties principales.
Traditionnellement, les moules à injection étaient coûteux à fabriquer et n’étaient utilisés que dans des productions à volume élevé (milliers de pièces). Aujourd’hui plusieurs choix sont possibles : moules construits en acier trempé, en acier pré-trempé, en aluminium et / ou en alliage béryllium-cuivre. Le choix du matériau du moule est avant tout économique.
La fabrication en acier coûte généralement plus cher, mais offre une durée de vie plus longue qui compense un coût initial plus élevé. Les moules en acier pré-trempé sont moins résistants à l’usure et sont principalement utilisés pour des volumes plus faibles ou des composants plus grands. La dureté de l’acier pré-trempé est généralement de 38-45 sur l’échelle Rockwell-C (HRC). Les moules en acier trempé sont soumis à un traitement thermique après usinage, ce qui les rend supérieurs en termes de résistance à l’usure et de durée de vie. La dureté typique varie entre 50 et 60 HRC.
Les moules en aluminium coûtent beaucoup moins cher que les moules en acier. Les moules en aluminium permettent des cycles plus rapides grâce à une meilleure dissipation de la chaleur. Ils peuvent également être renforcés en fibre de verre. Le cuivre au béryllium est utilisé dans les zones du moule qui nécessitent une élimination rapide de la chaleur ou dans les zones qui génèrent de la chaleur liée au cisaillement.
Choix de la matière la mieux adaptée au moulage par injection
La plupart des polymères peuvent être utilisés, y compris les thermoplastiques et certains élastomères.
Les matériaux sont choisis en fonction de leur résistance, de la fonction de la pièce à fabriquer, mais aussi des paramètres de moulage.
Il est possible d’injecter d’autres matériaux comme des alliages d’aluminium ou de zinc (Zamak). @plastisem
2. Comment éviter les principaux défauts liés à l’injection plastique ?
Avant de lancer la fabrication du moule, vous aurez validé quelques pièces prototypes. L’impression 3D permet aujourd’hui de réaliser, à moindre coup, des modèles qui vous permettront de consolider votre conception.
Ne pas hésiter à se rapprocher d’un mouliste, qui saura vous conseiller.
Sont abordés ici des défauts liés à la conception et non pas ceux principalement dus au moule ou au process de fabrication :
- Cloques : moule trop chaud
- Décoloration : mauvais mélange de la matière et du colorant
- Marques de frottement : état de surface du moule, dépouilles
- Bavures au plan de joint : force de fermeture trop faible
- etc…
Le positionnement des points d’injection dans le moule est un facteur influent sur le résultat final. Cela modifie l’écoulement de la matière fondue. L’empreinte du moule doit être complètement remplie.
Une définition importante : Les contraintes, et contraintes résiduelles
Lorsqu’une résine plastique est fondue avant l’injection, les liaisons moléculaires du matériau sont temporairement brisées en raison de la chaleur et de la force de l’extrudeuse. Cela permet aux molécules de s’écouler dans le moule. Les liaisons se reforment ensuite à mesure que le matériau refroidit, mais les contraintes sur le matériau demeurent.
Ces contraintes de pièce peuvent causer des gauchissements, des marques de creux, des retassures, des fissures, une cassure prématurée ou d’autres problèmes.
Certaines contraintes sur une pièce moulée par injection sont prévisibles, vous devez concevoir vos pièces avec le plus grand soin possible pour diminuer ces contraintes. Il faudra ajouter des transitions douces entre les différents volumes du moule et utiliser des arrondis et des congés dans les zones à fortes contraintes. Un cahier des charges exemple pour la conception de vos produits vous permettra de standardiser vos process de fabrication.
Épaisseur des parois de la pièce :
C’est un point de conception essentiel : il faut privilégier l’épaisseur constante des « murs » de la pièce. Eviter les fortes variations d’épaisseur avec des parois adjacentes. Ceci afin de favoriser le refroidissement homogène de la matière. Cette caractéristique peut avoir des effets importants sur le coût, la vitesse de production et la qualité des pièces finies.
Épaisseur de paroi appropriée :
L’objectif est généralement de choisir le mur le plus mince possible. Les parois minces utilisent moins de matériau, ce qui réduit les coûts et prend moins de temps à refroidir, ce qui réduit le temps de cycle.
L’épaisseur minimale de la paroi dépend de la taille et de la géométrie de la pièce, des exigences structurelles et du comportement de la résine en matière d’écoulement. Les épaisseurs de paroi d’une pièce moulée par injection sont généralement comprises entre 2 et 4 millimètres. Elles peuvent descendre jusqu’à 0,5 mm.
Lorsque la section épaisse se refroidit, alors elle se contracte vers la section plus mince déjà solide. Cela provoque une déformation, une torsion ou une fissure à l’endroit où les deux sections se rencontrent. Pour éviter ce problème, essayez de concevoir des murs uniformes dans toute la pièce. Quand ce n’est pas possible, le changement d’épaisseur doit être aussi graduel que possible. Les variations d’épaisseur de paroi ne doivent pas dépasser 10% dans les plastiques à fort retrait. Les transitions d’épaisseur doivent être effectuées progressivement, de l’ordre de 3 à 1. Cette transition progressive évite les concentrations de contraintes.
retassures :
gauchissement :
Tableau de retrait de matière pour les plastiques :
Ce tableau indique le taux de retrait que subit un plastique lors de son refroidissement et de sa solidification après le moulage. Ce taux varie selon le type de plastique et peut être influencé par d’autres facteurs tels que la température de moulage, la pression, l’épaisseur de la pièce, et les conditions environnementales.
Dépouille :
La dépouille est le choix technique qui est retenu pour pouvoir éjecter la pièce du moule sans la casser et sans fournir trop d’efforts. Mais attention car cela modifie sa géométrie. Toutes les parties verticales seront dépouillées.
- Utilisez au moins 1 degré de dépouille pour toutes les surfaces verticales
- ½ degré de dépouille pour les « petits » mur (faible hauteur)
- 2-3 degrés de dépouille fonctionnent très bien dans la plupart des situations
- 3 degrés de dépouille est un minimum pour une zone d’arrêt : métal du moule glissant sur le métal.
Si l’on applique une texture sur une zone, plus le grain est épais, plus il faudra de dépouille ( 5° voir plus )
Un point sur les éjecteurs
Lors de l’injection du plastique dans l’outillage, la matière va être soumise à de très fortes pressions qui vont la compresser. Pendant le refroidissement, cette dernière va se rétracter de 0,5% à 3,0%. Pour démouler la pièce, il faudra donc la pousser via des éjecteurs guidés par une batterie d’éjection. La force nécessaire pour sortir la pièce peut atteindre plusieurs tonnes (pour de grosses pièces). Les éjecteurs vont alors laisser sur la partie intérieure de la pièce de petites traces de forme ronde ou rectangulaire. Cela se produit aussi lorsque le temps de refroidissement est trop court et que le plastique n’a pas eu suffisamment de temps pour durcir. Il faudra choisir le côté de la pièce où il est possible de laisser ces marques sans altérer l’aspect ou les propriétés techniques.
Le marché du moulage par injection plastique est en expansion.
Ce marché est stimulé par la demande croissante de composants en plastique provenant de divers secteurs tels que l’emballage, l’automobile, les appareils ménagers, les dispositifs médicaux, l’électricité ou l’électronique.
L’industrie automobile augmente sa demande d’objets légers et durables pour remplacer les pièces métalliques lourdes, et ainsi réduire la consommation de carburant des véhicules.
Dans de nombreux domaines le plastique est devenu indispensable et la part des matériaux biosourcés reste marginale. Une partie des pièces fabriquées en plastique ne sont pas recyclables.
3. Quelle matière choisir pour un boitier électronique avec PCB ?
Le choix de la matière pour un boîtier en plastique dépend de plusieurs facteurs tels que la résistance mécanique, la résistance chimique, la température d’utilisation, l’aspect esthétique, la facilité de fabrication, etc.
En général, pour un boîtier électronique, il est recommandé d’utiliser des matériaux thermoplastiques tels que le polycarbonate, l’ABS ou le nylon. Ces matériaux sont résistants aux chocs, légers et faciles à mouler par injection. Ils sont également disponibles dans une variété de couleurs et peuvent être traités pour améliorer leur résistance aux rayures et aux intempéries.
Le polycarbonate est souvent choisi pour sa résistance élevée aux chocs et sa transparence, ce qui en fait un choix populaire pour les boîtiers de produits électroniques tels que les appareils photo et les smartphones. L’ABS est un matériau économique et résistant aux chocs qui peut être facilement moulé avec une finition lisse. Le nylon est un matériau durable et résistant à l’usure qui est souvent utilisé pour les boîtiers d’outils électriques.
Il est important de prendre en compte les exigences spécifiques de votre application avant de choisir un matériau pour votre boîtier électronique en plastique. Il peut être utile de consulter un expert en plasturgie pour vous aider à choisir la matière la plus appropriée pour votre projet.